An Optimization of quantity for Loading: A case study of Thanapiriya Co., Ltd.
Abstract
The purpose of this research is toarrangement suitable for loading in the transportation and product distribution by using the product arrangement method by considering the volume of goods of the truck for transportation to various branches of Thanapiriya Public Company Limited, which the sample group is the type of each vehicle, divided into 4 small wheels, 6 medium wheels trucks , 6 big wheels, 6 extra large wheels and 10 wheels with different payloads of 24 vehicles, and the goods transported between the 21 branches and 12 district customers by considering the average and the standard deviation of the volume of remaining space. the problem model using the Bin Packing Problem and the best way to find the optimization answer by comparing 3 methods: LP Simplex, Particle Swarm Optimization (PSO) and Genetic Algorithm (GA) to find suitable trucks for the quantity of products and remaining minimal space in the cabinet.
The results of the research found that when comparing the remaining space from the original model to the mathematical analysis of 3 methods, can reduce the space in the truck and reduce the number of trucks from the original appearance as follows. Reducing space in the truck from the original analyzing range 1, LP Simplex can be reduced to 1,831.7 m3.
The method of PSO can be reduced by 1,685.58 m3 and the GA can be reduced by 1,699.47 m3. Analysis of range 2, LP Simplex can reduce 1,703.98 m3, the PSO can be reduced by 1,400.58 m3 and the GA can reduce 1,511.21 m3. Reducing of the number of trucks from the old model, by analyzing the first phase at 15 cars and analysis of the second phase at 28 cars.
References
Bischoff, E. E., & Marriott, M. D. (2017). A comparative evaluation of heuristics for Container
Loading. European Journal of Operational Research,44(2), 267-276
Blazewicz et al. (1996). Scheduling Computer and Manufacturing Processes. Berlin: Springer, 1996b.
Blum, C., & Roli, A. (2003). Metaheuristics in combinatorial optimization: Overview and Conceptual comparison. ACM Computing surveys, 35(3), 268-308.
Chien, C. F., Zheng, J. N., & Gen, M. (2015). Multi-Objective Multi-Population Biased Random-Key Genetic Algorithm for the 3-D Container Loading Problem. Computers & Industrial Engineering, 89, 80-87
Dyckhoff, H., (1990). A typology of cutting and packing problems. European Journal of Operational Research, 44, 145-159.
Gonçalves, J. F., &. Resende, M. G. C. (2013). A Biased Random Key Genetic Algorithm for 2D and 3D Bin Packing Problems. International Journal of Production Economics, 145, 500-510
Kang, K., Moon, I., & Wang, H. (2012 ). A hybrid Genetic Algorithm with a New Packing Strategy for the Three-Dimensional Bin Packing Problem. Applied Mathematics and Computation, 219, 1287-1299.
Piyachayawat, T., Mungwattana, A., & Supithak, W. (2017). An Evolutionary Algorithm for solving the Multi-Size Pallet Loading Problem in a Lamps and Lighting Factory: A Case Study. Thai Journal of Operations Reseach, 5(1), 48-59 [in Thai]
Praditwong, K., & Talethong, T. (2016). Genetic Algorithms with Local Search to Solve Three Dimensional Bin Packing. Veridian E-Journal, Science and Technology Silpakorn University, 3(6), 43-56.[in Thai]
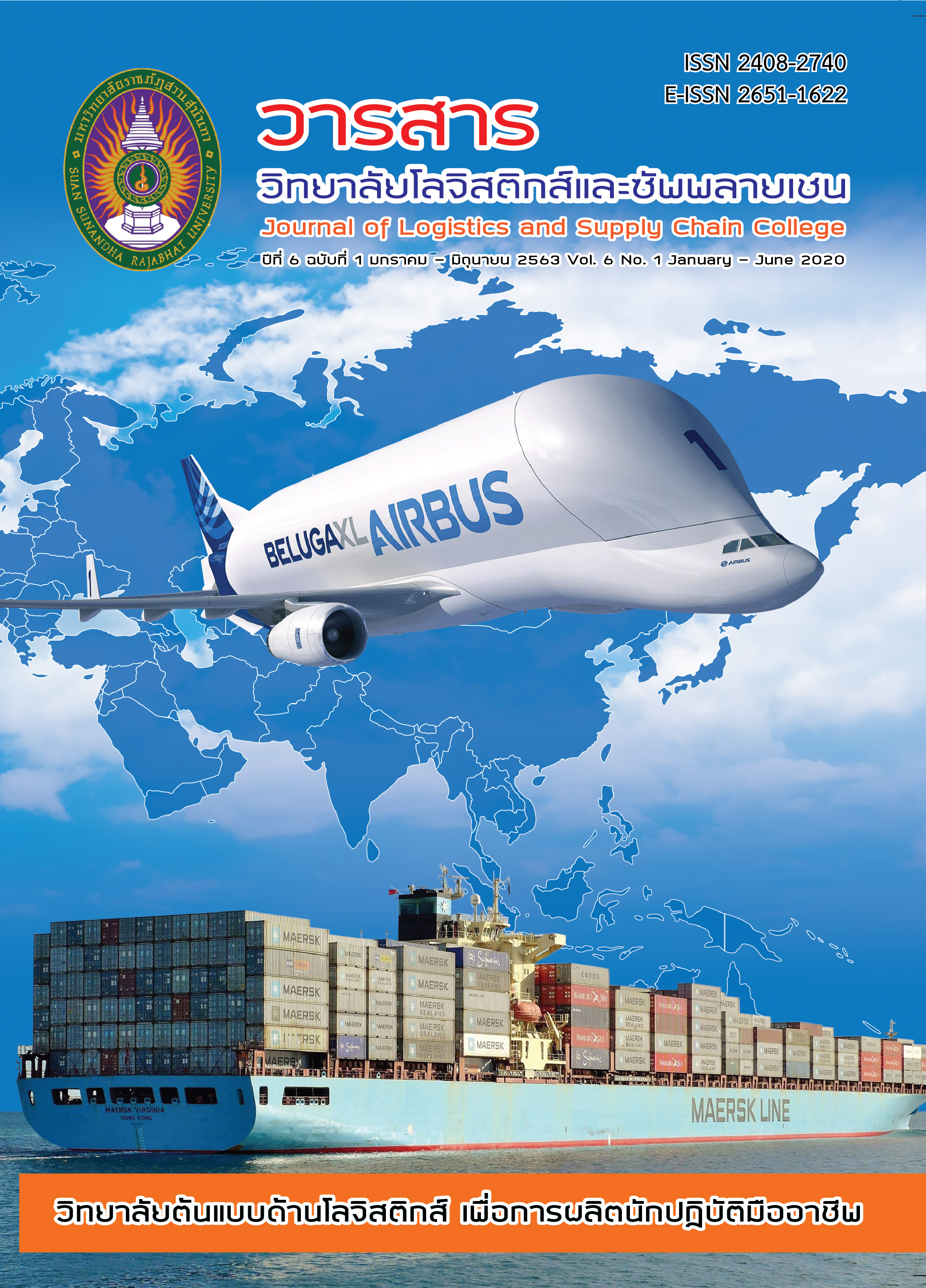